Review of Twin Screw Extrusion Parameters That Impact TiO2 Dispersion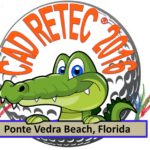
Philipp Niedenzu
Principle Investigator
The Chemours Company
Twin screw extrusion processes have long been a staple of the plastics manufacturing industry. Masterbatch compounding processes are the primary means of incorporating titanium dioxide into plastic melts, particularly so for polyolefins. The majority of twin screw compounding processes are optimized for low solids content and the very specialized field of high solids compounding remains largely unexplored in the masterbatch compounding market. One mystery of high solids compounding, especially with materials such as TiO2 pigment, is the role of process parameters with respect to pigment dispersion. The paper demonstrates how temperature and the ratio of feed rate/ RPM (Q/N), are pre-determinants for the dispersion quality using a given screw design. The paper utilizes computer simulation to highlight the impact of screw design and how the screw design impacts the fill factor, residence time distribution and viscosity. The impacts are then linked with a sieving dispersion test to characterize the level of agglomerates in a 70% TiO2 formulation in LDPE.
Biography – Philipp Niedenzu
Philipp Niedenzu received his Ph.D. degree from the Ohio State University in inorganic chemistry in 1991. Since then, he has been working in the performance chemicals industry for over 20 years in a variety of technical and innovation roles within DuPont and Chemours. He worked for two years performing fundamental research for the DuPont Titanium Technologies department. Thereafter, he re-located to the TiO2 manufacturing site in Tennessee and led several product development efforts for the plastics application. After working at a manufacturing site for seven years, he transferred to Mechelen, Belgium and acted as a technical consultant for the use of TiO2 in plastics applications within the European market. After five years of consulting work, Philipp relocated to Wilmington, Delaware to join the Global Plastics Offering department with responsibility for new offering development in the plastic applications and market analysis of titanium dioxide use in plastics. He is currently in the Product Technology Research & Development team for Chemours Titanium Technologies in Wilmington, Delaware. He is certified as a six sigma black belt and is a named inventor on multiple United States patent applications.