Improved Dispersion of Organic Pigments in Masterbatch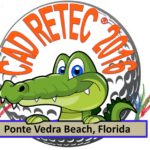
Robert Roden
SteerAmerica
When using co-rotating twin screw extruders, the concentration (weight %) of organic pigments in masterbatch formulations is usually limited by the ability to disperse the organic pigment. As the content of the pigment increases it becomes more difficult to disperse the pigment. This often limits the concentration of pigment in masterbatch to 20% or less. As is typical with other color and additive masterbatch formulations it is desirable to maximize the content of the pigment or additive. Optimal dispersion of the pigment is dependent on shear energy required to break down agglomerates and reduce particle size to the primary aggregate or particle size of the pigment. A characteristic of organic pigments is that if too much compression is applied to the pigment prior to wetting it results in the creation of large agglomerates that are extremely difficult to break down and disperse without multiple passes through the extruder. The typical 2 lobe kneading blocks that have been used to wet and disperse pigments for decades, and used in most masterbatch extruders today, creates pockets of high compression to generate shear for dispersion. Raw pigment that is exposed to this compression can agglomerate. Agglomerate formation of the pigment after being introduced into the extruder is often misinterpreted to be inadequate dispersion of the pigment. Proper wetting of the pigment prior to compression and the utilization of kneading screws that produce needed shear while reducing or eliminating the incident of high compression can enable the production of high concentration organic pigment masterbatch.
Biography – Robert Roden
Robert has many years of experience in thermoplastics R&D and manufacturing, holding technical and managerial positions in the Dow Chemical Co. and General Electric Co. He has held a position as a business development manager within the US Defense industry. He has directed research for the US Army in areas as diverse as conductive ceramics to ballistic composites manufacturing. He has been technical manager for two major OEM suppliers of plastics manufacturing equipment and is currently the Associate Vice President for STEERAmerica and Global Head for Manufacturing Technology.